Next Gen Technology – Digital Twin
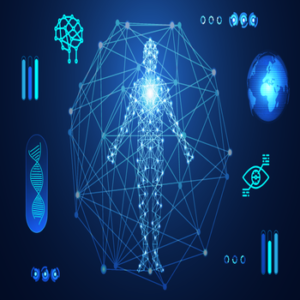
Here, we are going to learn something that will dominate the technology world in the near future. In addition, how to construct it, where it is utilized, and ongoing research updates relating to it are offered for your up-to-date understanding.
What’s the most valuable commodity we have in today’s modern world? The answer is TIME. We strive to spend less time on unnecessary actions, automating repetitive processes, and speeding up how we discover solutions. Businesses are losing billions on wasted opportunities or have passed the point of no return for structural and product changes. The size of the company is correlated with the complexity of the Product Life Cycle (PLC) they have. Highly automated manufacturing machines are tightly connected with human processes, supply chains, and logistics. Global industrial leaders are searching for solutions that help them manage, control, support, and develop competitive products. The key lies in the Internet of Things (IoT) and the technology which is lies in this article.
Imagine being able to replicate a system and, through doing this, possibly predict its future. Are you able to identify the technology? The technology is Digital Twin, as you correctly said.
A digital twin is a digital representation of a physical object, process or service. A digital twin can be a digital replica of an object in the physical world, such as a jet engine or wind farms, or even larger items such as buildings or even whole cities.
Understanding Product Performance
Digital twins give businesses an unprecedented view into how their products perform. A digital twin can help identify potential faults, troubleshoot from afar, and ultimately improve customer satisfaction. It also helps with product differentiation, product quality, and add-on services, too.
If you can see how customers are using your product after they’ve bought it, you can gain a wealth of insights. That means you can use the data to (if warranted), safely eliminate unwanted products, functionality, or components, saving time and money.
Why and How to Design Digital Twins?
The digital twins can be created for a wide range of applications, for example, to test a prototype or design, assess how a product or process will work under different conditions, and determine and monitor lifecycles.
A digital twin design is made by gathering data and creating computational models to test it. This can include an interface between the digital model and an actual physical object to send and receive feedback and data in real time.
Data
A digital twin requires data about an object or process in order for a virtual model to be created that can represent the behaviors or states of the real world item or procedure. This data may relate to the lifecycle of a product and include design specifications, production processes or engineering information. It can also include production information including equipment, materials, parts, methods and quality control. Data can also be related to operation, such as real-time feedback, historical analysis and maintenance records. Other data used in digital twin design can include business data or end-of-life procedures.
Modelling
Once the data has been gathered it can be used to create computational analytical models to show operating effects, predict states such as fatigue, and determine behaviors. These models can prescribe actions based on engineering simulations, physics, chemistry, statistics, machine learning, artificial intelligence, business logic or objectives. These models can be displayed via 3D representations and augmented reality modelling in order to aid human understanding of the findings.
Linking
The findings from digital twins can be linked to create an overview, such as by taking the findings of equipment twins and putting them into a production line twin, which can then inform a factory-scale digital twin. By using linked digital twins in this way it is possible to enable smart industrial applications for real world operational developments and improvements.
Research Perspective of Digital Twin
Researchers can explore in the following areas to gather more interesting benefits of the digital twin.
- Digital Twins in Metaverse
- AWS IoT TwinMaker
- Digital human twin
1.Digital Twins in Metaverse
The metaverse is rapidly expanding, and with that, several companies are responding by preparing for the virtual world. Whether they’re building virtual headquarters, factories, retail stores or products, companies are beginning to invest in digital twins of their entities in anticipation of the metaverse continuing to gain traction across the business landscape.
Since the invention of the internet, companies have had to adapt to the changing digital times with new technologies and new circumstances. The metaverse is no different, and while it may be difficult to wrap your head around, taking the time to learn about digital twins and how they fit into virtual reality can be very beneficial.
The metaverse itself acts as a digital twin to our universe and our reality, and what’s inside are more digital twins of tangible things that will eventually be used for transactions and optimizing business processes.
2. AWS IoT TwinMaker
Amazon Web Services IoT TwinMaker has capabilities for each stage of the digital twin building process: collecting data from diverse data sources using connectors (components), connecting to data where it lives to represent your digital twins, and combining existing 3D visual models with real-world data using a scene composition tool, and building web-based applications using a plug-in for Grafana and Amazon Managed Grafana that you can use to create dashboards.
With AWS IoT TwinMaker, customers can now derive previously unavailable insights about their operations that inform real-time improvements to their buildings, factories, industrial equipment, and production lines and make accurate predictions about system behavior with minimal effort.
AWS IoT TwinMaker is currently available in the US East (N. Virginia), US West (Oregon), Europe (Ireland and Frankfurt), and Asia Pacific (Singapore and Sydney) regions.
3.Digital Human Twin
Digital Twin in Healthcare
The future of healthcare needs to be built on early detection of disease – ideally even before any symptoms appear. But that’s easier said than done. How do you know which tests to do – and when? Regular thorough check-ups are only feasible for wealthy individuals who can afford to pay. And, even then, a disease could develop for months unnoticed in between check-ups.
The answer could lie in digital twin technology. If we each had a virtual representation of ourselves, including all our organs, in the form of a digital human twin, that virtual “being” could be constantly monitored to detect the very earliest signs of disease and automatically alert the healthcare system – stopping most diseases in their tracks.
How it works in healthcare?
Now attention is turning to the use of digital twin technology in healthcare. It holds the promise of making it easier to personalize medical treatment based on factors such as an individual’s unique genetic make-up, anatomy and behavior. The technology could also unlock more accurate monitoring of medical devices – and even model healthcare organizations to improve the way they deliver care.
Digital Human Twin
But a crucial step is to move towards detecting diseases as early as possible – by building a digital human twin. This needs a wide range of sensors to capture a variety of data points such as digital (sound, image, etc.), biophysical (blood, saliva, etc.) and behavioral (emotional state, language, etc.). These data points then need to be aggregated into a dynamic digital human twin that can monitor your health and alert the healthcare system as soon as something changes.
Digital human twins may sound like science fiction – but we actually already have all the right ingredients today.
Applications of Digital Twin in various fields
Benefits range from process efficiencies and higher productivity to moving to a sustainable and circular economy.
Aerospace: Airbus aims to cut its production lifecycle by 50% and is betting on digital twins to help it to achieve this ambitious goal. “For each new product, we are actually building four digital twins. We not only create a twin for that product; we also create one each for the related production equipment, production process, and service process. We simulate all these aspects before we actually start to build the product or the factory to manufacture it. This helps us significantly reduce our engineering lifecycle and cost in production,” says Peter Weckesser, former digital transformation officer at the Defense and Space arm of Airbus.[2]
Consumer products: Philip Morris International, PMI, has created a digital twin of its global manufacturing footprint. This allows the company to assess the impact of changes in product portfolio, market regulations, and even business disruption. The company has consequently reduced the use of spreadsheet simulations by 90% and was able to decrease the time required for scenario evaluation from weeks to hours.[3]
Automotive: BMW recently announced the design of a digital factory twin that can be used to simulate the operations of 31 separate factories. All elements – associates, robots, buildings, and assembly parts – can be simulated in this model, which is expected to produce planning processes that are 30% more efficient.[4]
Healthcare: Even more interesting applications of digital twins are being made in the healthcare sector. Dassault Systèmes’ Living Heart Project – a collaboration between industries, clinicians, and researchers, with members across 130 organizations in 24 countries – has developed the first 3D simulation of a living heart, allowing the development of testing paradigms for virtual insertion, placement, and performance monitoring of pacemakers and other cardiovascular devices.[5] Today, there is ongoing research into the use of digital twins for the planning of surgical procedures; optimizing drug dosage for patients; and even improving drug safety in the design and testing phases.[6]
Manufacturing: Kaeser, a German air-compressor manufacturer, implemented a digital twin system for its air stations. This provides operational data such as the air-consumption rate, which can then be monitored by its employees. This, in turn, allows the company to implement “servitization” – charging consumers on the basis of usage, rather than for the machine units themselves.[7]
Sustainability: Through simulations and scenario analysis, predictive modelling and operational efficiency, digital twins allow organizations to optimize their resource utilizations. For instance, Unilever is making use of digital twins at a facility in Brazil to make production more efficient. The company used a digital twin to set manufacturing parameters; for example, the temperature at which soap is pushed out before being cut into bars. The project resulted in a savings of USD2.8 million by reducing energy usage and improving productivity by 1% to 3%.[8] Further, digital twins also enable infrastructure owners/operators in making the buildings more sustainable.
For industries, the benefits from the use of digital twins span the lifecycle of a product. A few of these benefits are shown below:
Digital twin Challenges in Research Perspective
This section focuses on the difficulties associated with Digital Twins.
1) IT Infrastructure
The Digital Twin requires infrastructure that allows IoT and data analytics to succeed; these will facilitate the effective operation of a Digital Twin. The Digital Twin will fail to achieve its objectives unless it has a well-connected and well-thought-out IT infrastructure.
2) Useful Data
The following challenge revolves around the data required for a Digital Twin. It must be high-quality data with no noise and a continuous, uninterrupted data stream. If the data is poor and inconsistent, the Digital Twin may underperform because it is acting on poor and missing data. The quantity and quality of IoT signals are critical for Digital Twin data. To identify the right data is collected and used for efficient use of a Digital Twin, planning and analysis of device use are required.
3) Privacy and Security
It is obvious in an industry setting that the privacy and security issues associated with Digital Twins are a challenging issue. Because of the large amount of data they use, and the risk this poses to sensitive system data. To overcome this obstacle, the key enabling technologies for Digital Twins – data analytics and IoT – must adhere to current security and privacy regulations. Consideration of security and privacy for Digital Twins data helps to address trust issues with Digital Twins.
4) Trust
The challenges associated with trust are both from an organisation point of view and that of the user. To ensure that end-users and organisations understand the benefit of a Digital Twin, which will aim to overcome the challenge of trust, Digital Twin technology needs to be discussed further and explained at a foundation level. Another method for overcoming trust issues is model validation. It is critical to ensure that Digital Twins perform as expected in order to maintain user trust.
With more understanding, trust in Digital Twins grows. The enabling technology will provide greater insight into the steps that ensure privacy and security practises are followed throughout development, overcoming trust challenges.
5) Expectations
Despite the fact that industry leaders Siemens and General Electric (GE) are accelerating Digital Twin adoption, caution is required to highlight the challenges that exist for Digital Twin expectations and the need for more understanding. The need for solid foundations for IoT infrastructure, as well as a better understanding of the data required to perform analytics, will ensure that organisations use Digital Twin technology. It is also difficult to combat the notion that the Digital Twin should be used solely for current trends. The benefits and drawbacks of Digital Twins must be discussed in order to take appropriate action when developing Digital Twin systems.
6) Standardised Modelling
The next challenge in all forms of Digital Twin development is modelling such systems because there is no standardised approach to modelling. From the initial design to the simulation of a Digital Twin, a standard approach, whether physics-based or designed-based, is required. Standardized approaches ensure domain and user understanding while ensuring information flow between each stage of a Digital Twin’s development and implementation.
7) Domain Modelling
Another challenge resulting from the need for standardised use is ensuring that information relating to domain use is transferred to each of the development and functional stages of Digital Twin modelling. This ensures compatibility with domains such as IoT and data analytics, allowing the Digital Twin to be used successfully in the future.
These are important moving forward because they ensure that they are taken into account in the future development of Digital Twins.
Sources:
https://www.ibm.com/blogs/internet-of-things/iot-cheat-sheet-digital-twin/
https://www.infoq.com/news/2022/05/aws-iot-twinmaker-ga/
https://dashdevs.com/blog/product-owner-talks-20-digital-twins-service-companies/
https://www.capgemini.com/insights/research-library/capgemini-perspective-digital-twins/
I-CIO, “Airbus highlights critical success factors for digital transformation,” September 2019.
PR Newswire, “River Logic Partners with Philip Morris International to Create Digital Twin of the Company’s Global Manufacturing Network,” September 2020.
FierceElectronics, “BMW features digital factory twin at Nvidia GTC21,” April 2021.
Dassault Systèmes, “THE LIVING HEART PROJECT,” accessed September 15, 2021.
VentureBeat, “21 ways medical digital twins will transform healthcare,” July 2021.
Plant Services, “Developing a new business model by selling supply,” April 2019.
The Wall Street Journal, “Unilever Uses Virtual Factories to Tune Up Its Supply Chain,” July 2019.
Fuller, A., Fan, Z., Day, C., & Barlow, C. (2020). Digital twin: Enabling technologies, challenges and open research. IEEE Access, 8, 108952-108971. https://doi.org/10.1109/access.2020.2998358